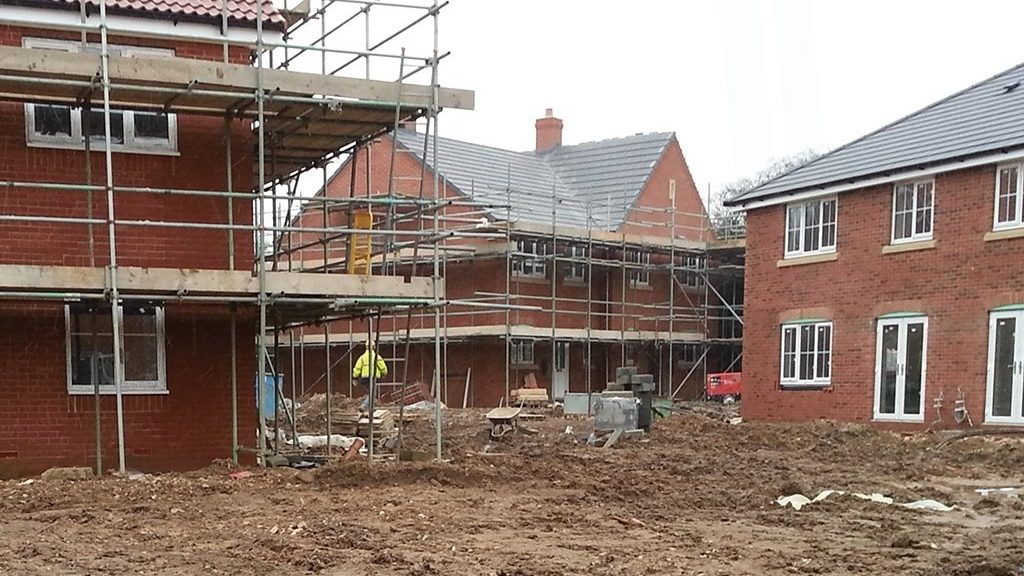
Searching for Sound Testing in London
Searching for Sound Testing in London
Unless plans were fully approved prior to 1 July 2003, sound testing will be required on your London development between rooms or spaces that share a common area of separating wall and/or floor as stipulated in Building Regulations Part E for the passage of sound. Sound Testing is not generally required for internal walls and floors within a dwelling-house, flat or room for residential purposes; however, all internal partitions should be designed to achieve 40dB.
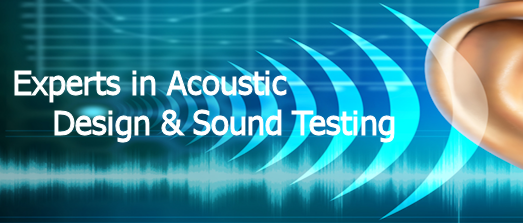
The buildings that require sound testing are:
1. Dwelling-houses, flats or rooms for residential purposes created by conversion of existing buildings or new build rooms for residential purposes will need to be tested if work starts after 1 July 2004.
2. New build dwelling-houses and flats will need to be tested if work starts after 1 July 2004.
The main aim of sound insulation testing in London is to ensure that minimum standards of sound resistance have not been compromised by poor workmanship and/or poor design. You are normally required to undertake sound testing to each type of construction, i.e. if you have a mixture of brick, blockwork, timber and metal studwork walls all four types would need to be tested, followed by a 10% sample of that type using the equipment shown in Plate A below.
For instance, if you have a project with 25 flats you would be required to do 3 x 6 pack of tests; each 6 pack contains 2 airborne wall, 2 airborne floor and 2 impact sound tests; however if any test failures occur, then the number of sound tests may need to increase on the development. When sound test failures occur, then the design and construction of the failed partitions will need to be revisited to try and evaluate the reasons for the failure; thereafter, agreement can be reached on how to rectify problem.
We have carried our hundreds of acoustic design reviews, so we are well placed to help you overcome any potential problems to achieve compliance with Building Regulations Part E.
When designing acoustic partitions you will need to consider the following:
a. The careful design of floor plans to avoid habitual rooms being placed side by side.
b. The mass and density of products that you are using.
c. Using good design detailing to ensure the careful isolation of materials.
d. The whole construction detail and how it is made up.
e. Undertaking careful acoustic detailing of junctions between walls, ceilings and floors.
f. Using acoustic wall ties in cavity walls.
g. Types of doors in sound resisting walls.
h. Containment of noise within noisy parts of a building such as lift shafts.
i. Positions of sockets and flues on opposite sides of walls to ensure they don’t sit back to back.
j. Sealing and filling of joints.
k. The use of cavity closers on window/door reveals.
l. Careful sealing of service penetrations.
m. Designing to reduce potential reverberation in common parts of buildings such as corridors and entrance areas and the subsequent use of absorbent materials.
Unfortunately unless the acoustic design has been taken into account, the floor and ceiling partitions can be the main pathways for sound transmission. The first type of sound transmission is airborne sound such as TV and speech; and the second is the passage of impact sounds such as footfall or children’s toys being dropped on the floor above. Achieving good airborne and impact sound isolation requires careful acoustic design considerations.
Plate A below shows one cost effective ceiling upgrade that can be undertaken on conversion projects. Firstly retain the existing floor joists, then above the joists install 22mm chipboard. Above the floor board install an acoustic resilient membrane and above this install the 22mm engineered floor. Within the joist cavity install 100mm AW IsoWool. To the underside of the joists fix a resilient hanger system and below this install two layers of 12.5mm sound boards ensuring that boards have adequate laps.
A simple Acoustic Floor Upgrade
To try and help our clients achieve compliance with Approved Document E, we offer the following 4 step acoustic design package:
1. Site Survey Visits – to let us view the existing site construction. This allows us to check for potential problematic construction such as inclusion of lightweight blocks in the existing construction. It also lets us check that the installation teams are installing the acoustic materials as per manufacturer’s guidelines.
2. Sample Sound Testing – of the existing construction. This offers an accurate overview of the acoustic performance of the existing partitions which enables us to offer a targeted acoustic design using the sound insulation performance of the existing construction.
3. Acoustic Design Review – a full design review of the proposed developments party walls and floors.
4. Pre-completion Sound Testing to satisfy Approved Document E.
APT Sound Testing can advise on all types of acoustic design, whether it’s accomplished during initial construction or during a refurbishment/renovation project.
We also undertake UKAS accredited sound testing providing a ‘one-stop’ solution for all your acoustic requirements. If you would like more information in regards to sound testing please follow our blog at: http://soundtestinguk.blogspot.co.uk or visit the APT Sound Testing website..