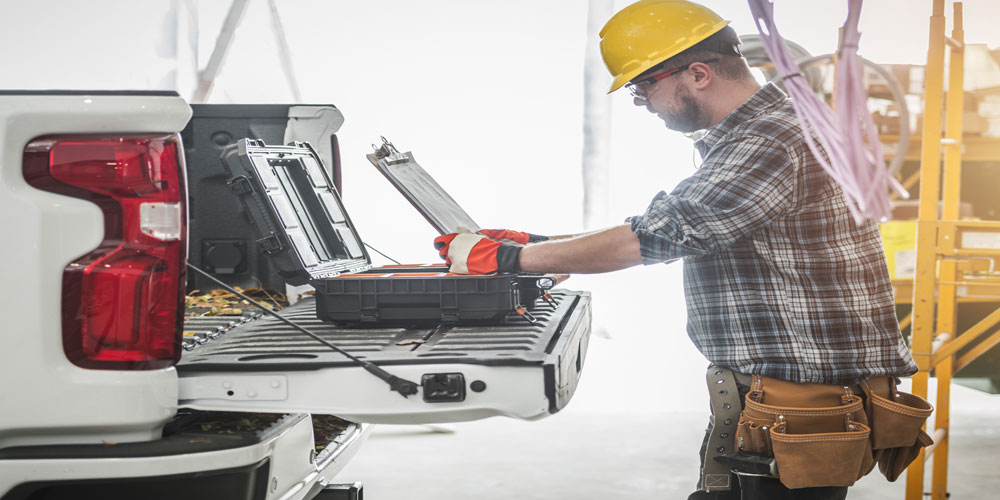
Air Tightness Testing in the Construction Industry
Air Tightness Testing in the Construction Industry: Ensuring Efficiency and Sustainability
In the ever-evolving construction industry, the focus on energy efficiency and sustainability has become paramount. As buildings strive to minimise energy consumption and reduce their environmental impact, air tightness testing has emerged as a crucial step in achieving these goals. By ensuring the integrity of a building’s envelope, air tightness testing plays a pivotal role in optimising energy performance, improving indoor air quality, and enhancing overall occupant comfort.
What is Air Tightness Testing?
Air tightness testing, also known as blower door testing, is a diagnostic procedure used to measure the air leakage of a building. It involves creating a pressure differential between the inside and outside of the structure while measuring the airflow that occurs as a result. This test helps identify areas of air leakage, such as gaps, cracks, and poorly sealed openings, allowing for targeted remediation and improved building performance.
Why is Air Tightness Important?
1️⃣ Energy Efficiency: Uncontrolled air leakage in a building can significantly impact its energy efficiency. Air infiltration can lead to heat loss during colder months and heat gain during warmer months, forcing heating and cooling systems to work harder and consume more energy. By conducting air tightness testing, construction professionals can identify and address these inefficiencies, resulting in reduced energy consumption and lower utility costs.
2️⃣ Indoor Air Quality: Air leakage not only affects energy efficiency but also impacts indoor air quality. Unfiltered air entering a building can introduce contaminants, allergens, and pollutants, compromising the health and comfort of occupants. By minimising air infiltration through air tightness testing, construction projects can ensure healthier indoor environments and promote occupant well-being.
3️⃣ Comfort and Thermal Performance: A tightly sealed building envelope reduces drafts and temperature variations, enhancing occupant comfort. By eliminating cold spots near windows, doors, and other vulnerable areas, air tightness testing contributes to maintaining consistent indoor temperatures and reducing the need for excessive heating or cooling.
4️⃣ Sustainability and Environmental Impact: As the construction industry strives to minimise its environmental footprint, air tightness testing plays a significant role in achieving sustainability goals. By reducing energy consumption, buildings with improved air tightness contribute to a lower demand for fossil fuel resources, resulting in decreased greenhouse gas emissions and a smaller carbon footprint.
How is Air Tightness Testing Conducted?
Air tightness testing involves the use of a specialised equipment called a blower door. The blower door consists of a calibrated fan installed in an external doorway or window, a pressure gauge, and various seals and accessories. The procedure typically involves the following steps:
1️⃣ Sealing Openings: All external doors, windows, vents, and other openings are closed, and internal doors are opened to allow for air circulation within the building.
2️⃣ Creating Pressure Differential: The blower door fan is activated to depressurise or pressurise the building. This creates a pressure differential between the interior and exterior, allowing for the measurement of air leakage.
3️⃣ Measuring Airflow: The pressure gauge connected to the blower door fan measures the airflow required to maintain the desired pressure differential. This measurement provides an indication of the building’s air tightness.
4️⃣ Identifying Air Leakage: During the test, construction professionals may utilise smoke pencils or infrared cameras to detect areas of air leakage. This information helps target specific areas for remediation and sealing.
5️⃣ Remediation and Retesting: Based on the results of the air tightness test, necessary repairs and improvements are made to reduce air leakage. Once remediation is complete, a retest is conducted to ensure the desired air tightness level has been achieved.
Benefits of Air Tightness Testing for Construction Professionals:
✅ Compliance: Many building codes and standards now require air tightness testing to meet energy efficiency and performance criteria. By conducting these tests, construction professionals can ensure compliance with regulations and obtain necessary certifications.
✅ Quality Assurance: Air tightness testing serves as a quality assurance measure, ensuring that the construction process meets the required standards. It helps identify potential issues early on, allowing for timely corrections and avoiding costly rework.
✅ Client Satisfaction: Buildings with improved energy efficiency, reduced utility costs, and enhanced comfort provide increased satisfaction to clients. By incorporating air tightness testing as part of their construction process, professionals can offer their clients a more sustainable and efficient end product.
In a world increasingly focused on sustainable development, air tightness testing has become a vital tool for construction professionals. By optimising energy performance, improving indoor air quality, and enhancing occupant comfort, air tightness testing not only benefits the environment but also contributes to the long-term success of construction projects. Embracing this practice is a step toward a greener and more sustainable future for the construction industry.