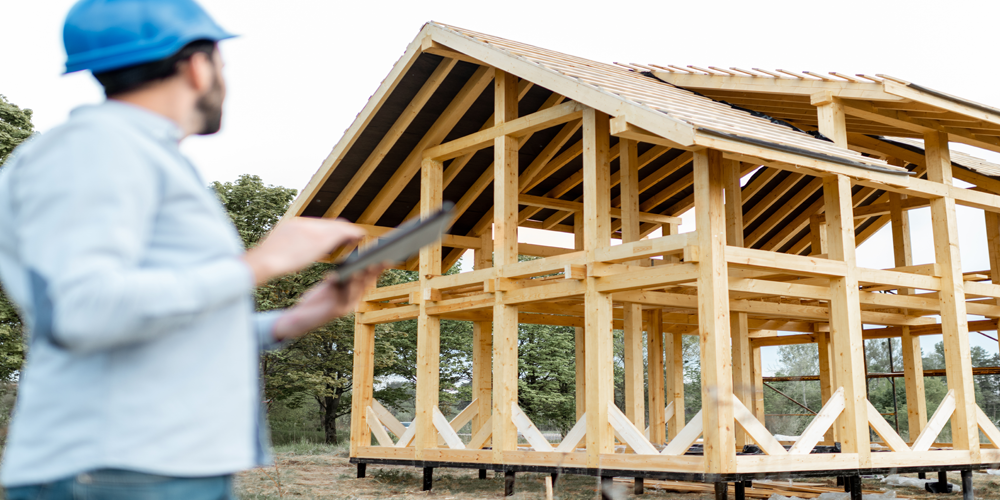
Air Tightness Testing on all New Dwellings
Is Air Tightness Testing Mandatory on all New Dwellings?
Yes! From June 2022 all new builds need to demonstrate a minimum level of air permeability of 8m³/h.m²; however, this figure is often lower to align with the design stage SAP assessment. There won’t be an option to undertake ‘sample testing’ with the new Building Regulations Part L, it will be mandatory to undertake air testing to all dwellings on your project.
The final air permeability is done through an onsite, pre-completion air tightness test. The design air permeability for a particular building may need to be lower to achieve the overall carbon emission rate for the building via and/or within an employer’s requirements/specification.
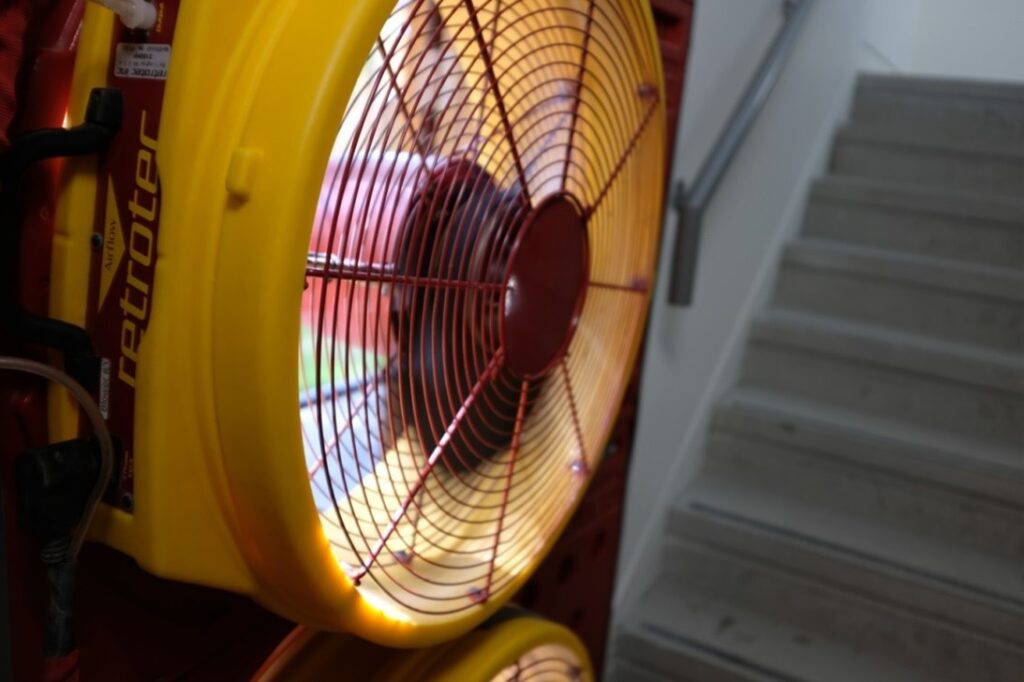
Should I undertake sample air testing on a show home?
Its good practice to undertake an air test on a sample unit, such as show home/s – to check that they can pass the air test, as any problems identified during the test can be highlighted and addressed on future units. As show homes are often the first building to be completely finished it’s a good place to start. We often visit sites at the end of the project, where no thought has been given to air tightness which leads to unts failing the air testing, which leads to costly and disruptive remedial work.
Avoid Leaky Buildings
The quality of a buildings construction and design will have a major effect on the amount of air leakage through a building’s fabric. If a building is leaky, it can create a drawing effect, pulling air in through gaps in the ground floor and walls especially if the buildings is turned up high. This may result in cold untreated air being drawn into the home through gaps on the ground floor, walls and ceiling resulting in cold draughts. Treated ‘warm’ air leaking out through gaps in the dwelling’s fabric is one of the main causes of heat loss and wasted energy.
The main disadvantages of leaky dwellings are:
Damage to Building Fabric – Excessive air leakage can allow damp air to penetrate the building fabric, causing mould and the effectiveness of the insulation. It can also lead to an increase in dust and pollen.
Raised CO2 emissions – A leaky dwelling will result in higher emissions, if a house has an air leakage rate of 10m³/h.m², as opposed to 5m³/h.m² you may be losing over 1/3 of your heating into thin air.
Inadequate heating – The increased heat loss will mean that the correctly designed/sized heating system may not be able to attain the required temperatures. it also means that extra load will be placed on the heating system thus shortening the lifespan of the system.
Discomfort – Excess draughts and localised cold spots can cause major discomfort. In extreme cases, excessive infiltration may make rooms uncomfortably cold during the winter months and too hot during the summer months, which often leads to complaints from residents.
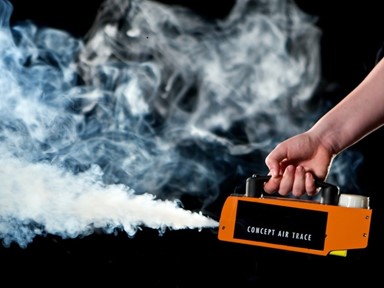
The benefits of an airtight buildings
There are many benefits for lowering the air tightness rate in new and existing buildings, they are:
- Lower energy costs for the lifetime of the building.
- Less chance of ongoing damage due to the reduced risk of interstitial condensation within the building fabric.
- Lower initial capital costs due to downsizing of plant and equipment required for heating/cooling.
- A longer life cycle for the plant and equipment as it doesn’t need to work as hard to maintain target termperatures.
- A safer building as fire compartments as well as external envelopes should be more robust.
- The building environment should be less drafty and potentially warmer and/or cooler as required.
- A raise in staff productivity – a happier worker is a usually a more productive worker.
The most common air leakage paths
There can be literally hundreds of air leakage paths within the home which can lead to air test failures. however, in our experience (having undertaken thousands of air leakage tests) these are the most common problem Areas:
- Floors – Unsealed wall/floor junctions can be a major area of air leakage. Also, services such as water pipes, gas pipes and electric cables that pass through external floor can also leak air.
- External Walls – Air can escape through the external walls, around areas such as joists that are built into the wall, unfinished mortar joints, service pipes, water pipes, gas pipes, boiler flues and electric cables that pass through external walls. They are often hidden behind kitchen cupboards, bath panels, sink pedestals, toilet basins. Also, draughts in bathrooms are much more noticeable and are particularly uncomfortable for occupants.
- Roof Spaces – Leakage into ceiling voids and the roof space. Air can leak past a poorly fitting loft hatch from the unheated roof void. Light fittings and gaps around them can offer a path into the roof void and also into the void between the ceiling and the next floor. Also, eaves cupboards can be a major area of air leakage as well as waste stacks and other service penetrations.
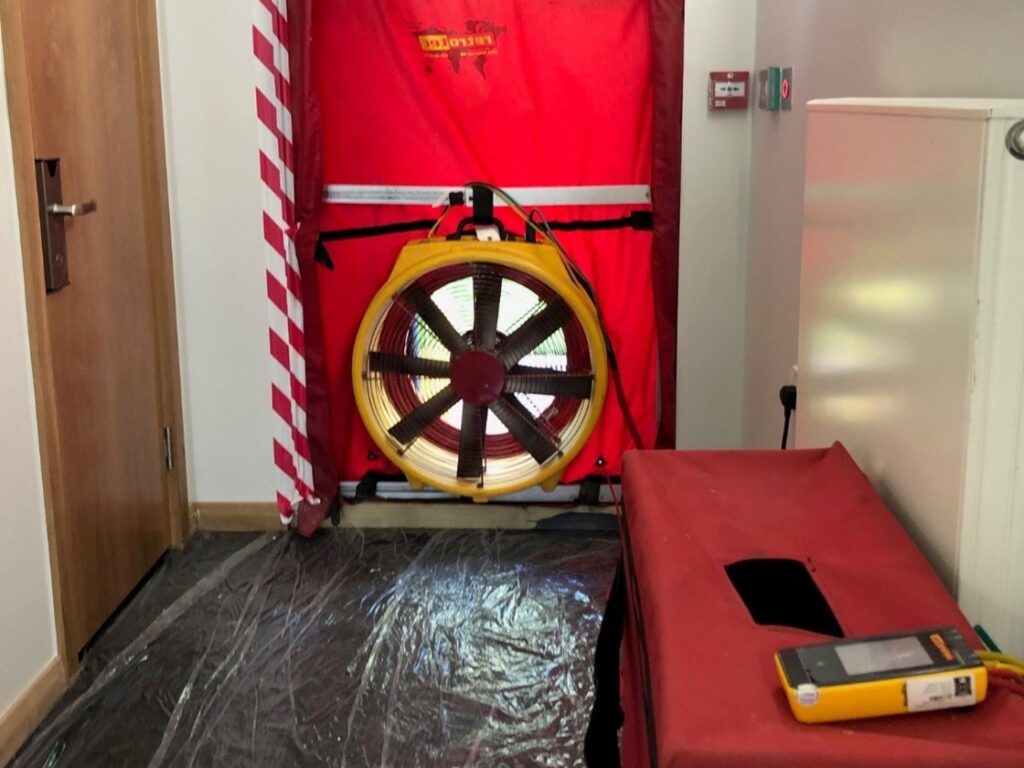
Where do I find more information on Air Tightness Testing?
There are many places to find information in regard to Air tightness testing. Basically the testing is carried out in accordance with the procedures detailed in ATTMA TSL1 (Please use the website www.bindt.org for a free download) and BS EN:13829 (2001). ATTMA TS1 describes how to carry out the air test and the analysis required to determine the air permeability of the building under test. Air permeability is expressed as volume flow per hour (m3/hr/m2) of air supplied to the space per square metre (m2) of envelope area for an internal to external pressure difference of 50 Pa.
Also, Building Regulations Part L also offers lots of useful information in regards to Air Tightness Testing, such as which plots should be selected and what parts of the building can be temporally sealed etc. If you would like more information on how to prepare your building to pass an air tightness test then please download our air tightness checklist.
A summary of our air tightness test procedure
Our air tightness testing procedure involves connecting a fan, or a number of fans, to a suitable aperture such as a standard external doorway in the building envelope. a number of environmental readings are taken (temperature and barometric pressure) and then the fan is turned on to pressurise the building over a range of pressure differences – usually between 25-70Pa, in 5Pa increments. Air volume flow rate through the fan (equal to the air leaking through the building envelope) and the pressure difference across the building envelope are recorded at each fan speed. In calculating air permeability rate, corrections are made for temperature and barometric pressure.
Please Contact us for your Air Tightness Testing now
It’s our ongoing aim to help all customers throughout their design, construction and final precompletion air tightness stages. We are happy to provide you with general air leakage design advice for your building envelope and onsite guidance. Upon completion of your project, we provide Nationwide UKAS Accredited Tightness Testing for domestic and commercial buildings to help you demonstrate Building Regulation Part L Compliance.
If you would like more information on our air tightness testing service, then please visit our website at www.aptsoundtesting.co.uk or contact us at: info@aptsoundtesting.co.uk. To have a chat about your project please call: 01525 303905