Preparing your Building Fabric for a Heat Pump Installation
Preparing your building fabric for a Heat Pump installation
An air source heat pump is a device that transfers heat from the outside air to the inside of a house, using a refrigerant cycle. Air source heat pumps can provide heating and hot water for a home, using renewable energy and reducing carbon emissions; however, for the heat pump to work properly the building fabric needs to be performing correctly.
That’s where we can help, we can undertake a complete building fabric heat pump survey, to check it will be good enough for the heat pump to work at its optimal efficiency.
Thermal Imaging & Air Leakage Surveys to Building Fabrics
For an air source heat pump to work best, the house needs to be well insulated and airtight. This means that the heat loss through the walls, roof, and floors is minimised, and the heat pump can operate at lower temperatures and higher efficiency. Good Airtightness also prevents draughts and cold spots, which can make the house feel uncomfortable and increase the heating demand.
Therefore, a house should be airtight for air source heat pumps to work properly because it will reduce the heat loss, improve the comfort, and lower the running costs of the system. Airtightness can be achieved by using good quality windows and doors, sealing any gaps or cracks in the building envelope, and installing a mechanical ventilation system with heat recovery to provide fresh air without losing heat.
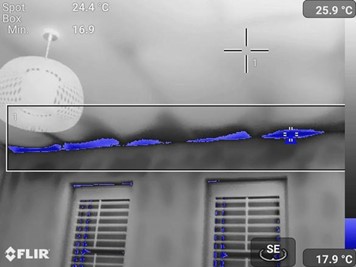
To try and help clients provide the optimum building fabric conditions prior to the air source heat pumps installation, we provide a combined thermal imaging and blower door air leakage survey to pinpoint any areas of missing insulation and air leakage paths within the building envelope.
Thermal imaging for checking the building fabric
Thermal imaging is a technique that uses infrared cameras to capture the temperature distribution of a surface or an object. Thermal imaging can help when checking your building fabric is properly prepared to install an air source heat pump, because it can:
- Identify the areas of heat loss and air leakage in the building envelope, which can reduce the efficiency and performance of the heat pump.
- Assess the continuity and quality of the insulation in the walls, roof, and floors, which can affect the heat demand and comfort of the building.
- Detect any defects or damages in the building fabric, such as cracks, dampness, or mould, which can compromise the structural integrity and durability of the building.
Thermal imaging can provide valuable information for improving the energy performance and airtightness of the building, which are essential for installing an air source heat pump. However, thermal imaging should be carried out by a qualified professional, who can interpret the results and provide appropriate recommendations. We can provide the thermal imaging using Level 3 Thermographers along with resolution (and sensitivity) Thermal Imaging cameras.
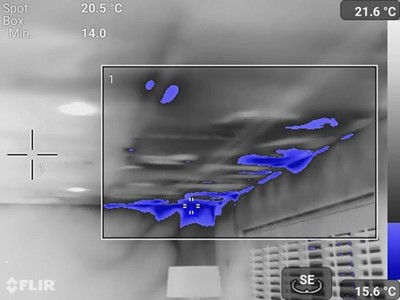
Air Tightness Testing for checking the building envelope
Air tightness testing and air leakage surveys are methods to measure and locate the amount of air that escapes or enters a building through gaps or cracks in the building fabric. These methods can help to the building fabric before the installation of the air source heat pump, because they can:
- Identify the areas of air leakage in the building envelope, which can reduce the air tightness performance of the building envelope, which will have a negative effect on the efficiency and performance of the heat pump.
- Assess the continuity and quality of the air leakage line within the building fabric, checking items such as windows, doors, walls/floor/roof junctions which can affect the ongoing heat demand and comfort of the building, especially in the colder months.
- Detect any defects or damages in the building fabric, such as unsealed areas around service penetrations which can cause dampness, or mould, which can compromise the structural integrity and durability of the building.
By improving the air tightness of the building fabric, the heat pump can operate at lower temperatures and higher efficiency, resulting in lower energy bills and carbon emissions. However, Air Tightness Testing should be carried out by a qualified professional, who can interpret the results and provide appropriate recommendations. As a UKAS and ATTMA accredited company, we can provide the air tightness testing to strict ISO standards using the latest high power door blower fans and smoke leakage equipment.
What are the Benefits of Combined Blower Door Thermal Imaging Survey?
The main benefits of using this method are:
- It provides a visual representation of the air leakage in a building, which can help to identify and locate the sources of heat loss, moisture problems, draughts, noise transmission and poor indoor air quality.
- It provides an air tightness test result, which can be compared against the heat pump manufacturers requirements.
- It allows for a more accurate diagnosis of the building envelope performance and helps to target remedial works more effectively and efficiently.
- It can help to achieve higher standards of energy efficiency, comfort, and health in buildings, as well as complying with regulatory requirements.
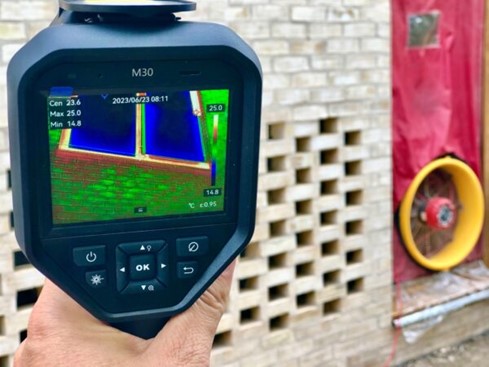
The savings of an airtight dwelling with ASHP
The energy savings from an air-tight house with an air source heat pump will depend on several factors, such as the quality of the insulation, the size and age of the house, the climate and the fuel type being replaced – here is some general estimates on the data from the Energy Saving Trust.
According to the Energy Saving Trust, installing a standard air source heat pump in an average three-bedroom semi-detached home in the UK (with radiator upgrades as required) can save up to £860 per year and 1,440 kg of CO2 if you are replacing an old gas boiler, or up to £1,460 per year and 2,320 kg of CO2 if you are replacing an old oil boiler. These figures are based on fuel prices as of Oct 2023.
However, the above approx. savings may vary depending on the efficiency and ongoing running cost of the heat pump, which will depend on the outside temperature, the heat demand of the house, and the electricity tariff. The Guardian reports that in a poorly insulated home, it may cost as much as 40% more to run a heat pump than a traditional boiler, because of the higher cost of electricity compared to gas. Therefore, it is important to improve the insulation and air tightness of the house before installing a heat pump, to reduce the heat loss and increase the savings.
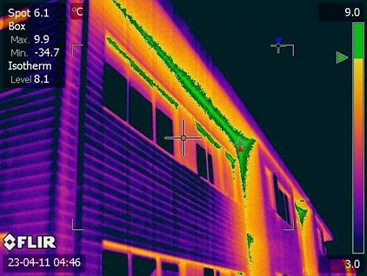
How to make your building more airtight to reduce heat loss.
There are many areas that can be improved in existing building fabric’s, prior to the installation of an air source heat pump system. Here is a list of the main air leakage paths within existing properties.
Improve external windows.
For external windows that open, purchase draught-proofing strips to stick around the window frame to fill the gap between the window and the frame. There are usually two types:
- Self-adhesive foam strips – these are cheap and easy to install but may not last long.
- Metal or plastic strips with brushes or wipers attached, which are long-lasting, but cost a little more and are usually the better option.
Make sure the weather strip is the right size to fill the gap in your window. If the strip is too big, it will get crushed, and you may not be able to close the window. If it’s too small, there will still be a gap and it will not be airtight.
For sliding sash windows it’s more awkward, foam strips do not work well. It’s best to fit brush strips or consult a professional. For windows that don’t open, use a silicone sealant. If you’re thinking of replacing your windows, consider installing energy efficient windows.
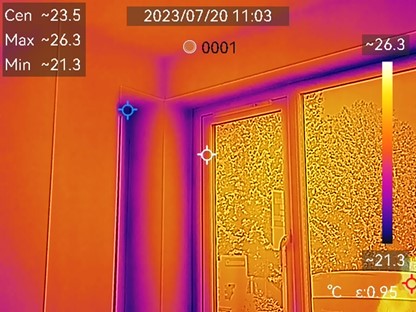
External Doors
Draught-proofing external doors can stop a lot of heat from escaping and will make your building more airtight and the upgrades shouldn’t cost you much. There are four main areas to consider when draught proofing your doors:
- Gaps around the perimeter of the door – fit foam, brush, or wiper strips like those used for windows. You will need to measure up the gap and size the weather seal accordingly.
- Gap at the bottom of the door – use a brush, rubber, or hinged flap draught excluder.
- Keyhole – buy a cover that drops a metal disc over the keyhole, these can be found at most hardware stores or online.
- Letterbox – use a letterbox flap; however, remember to measure your letterbox before you buy to ensure the sizing is correct.
If you have a room, you don’t normally heat, such as your conservatory, spare room or kitchen. Keep those doors closed to stop the cold air from moving into the rest of the house. If there is a gap at the bottom of the door, block it with a draught excluder as detailed above.
It’s worth noting that internal doors between heated rooms don’t need draught-proofing, as you don’t lose energy when warm air circulates between habitable spaces.
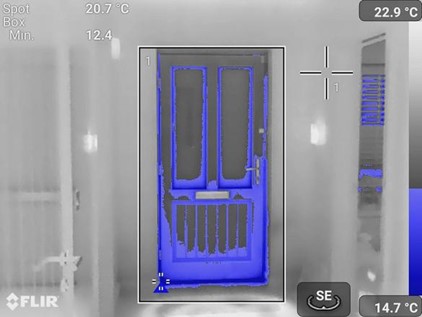
Chimneys
If you don’t use your fireplace, your chimney is probably a main source of unnecessary draughts and air leakage. There are two main ways to draught-proof a chimney:
- Fit a purpose made cap over the chimney pot – this should be done by a professional.
- Buy a chimney draught excluder – these helps stop draughts and heat loss through the chimney and are usually fitted inside the bottom of the chimney flue.
Please note remember to remove the temporary draught-proofing if you decide to light a fire.
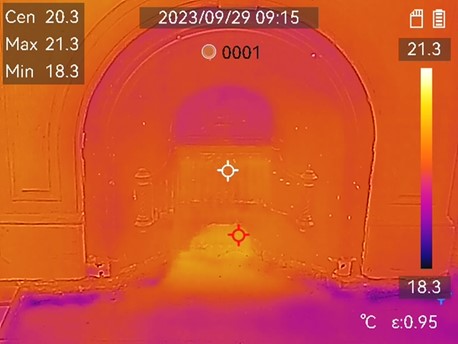
Skirting boards and Floorboards
You can seal cracks in floors by squirting filler into the gaps. Floorboards and skirting boards often contract at wall/floor junctions causing air leakage paths. Use a sealing material that can tolerate movement – these are usually silicone-based. Look for the following products:
- mastic-type products
- flexible fillers
- decorator’s caulk
Fillers come in different colours, and for indoor and outdoor use. They block gaps permanently so be careful when you apply them – wipe off any excess with a damp cloth before it dries. Fillers may break down over time but can easily be reapplied.
Check whether you also need to insulate between the skirting board and the floor. Find out more in our guide to floor insulation.
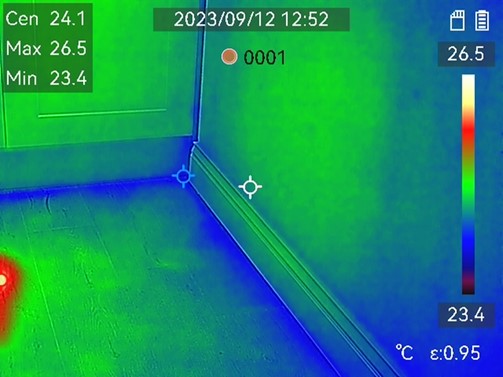
Loft hatches
Hot air rises and gets lost in the cold space in your loft or attic, cold air can also drift down in your warm space via draughts, so it’s worth blocking off gaps around your loft hatch. Use strip insulation, as you would on a door.
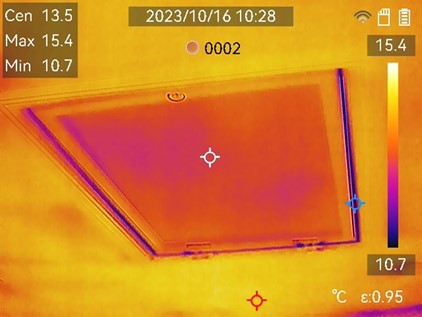
Pipework and cable penetrations
You can fill small gaps around pipework with silicone fillers, similar to the fillers used for skirting boards and floorboards. Fill larger gaps with expanding polyurethane foam. This is sprayed into the gap, expands as it dries, and sets hard. We have more information about insulating tanks, pipe work and radiators.

Old extractor fans
Old fan outlet penetrations may need to be filled with bricks or concrete blocks and sealed from both the inside and outside as this can be a major cause of air leakage.
Cracks in walls
You can fill in cracks using cements or hard-setting fillers. These will work around electrical fittings on walls and ceilings and at ceiling-to-wall joists. If there is a large crack in your wall, you may need to check if there’s an underlying problem. Consider consulting a surveyor or builder to see what caused the crack in the first place.
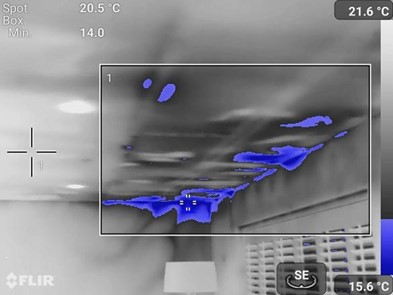
We can help with your combined blower door Thermal Imaging Survey
If you require a combined blower door thermal imaging survey for your building project, please contact us at: info@aptsoundtesting.co.uk. Or call Darren on 07775623464. We have qualified and experienced professionals who can provide you with high-quality service and advice.